Programmable Smart Chargers for Lead-Acid and Lithium Batteries
In recent years, batteries have become one of the most accessible energy storage solutions, now widely used in consumer electronics, power tools, uninterruptible power supply (UPS) systems, electric vehicles, and renewable energy storage.
However, the varying characteristics of different battery types pose challenges for both consumers and engineers when selecting the right batteries and chargers. This article explores the differences between the two most common battery types—lead-acid and lithium batteries—and provides an overview of how to choose the appropriate charger.
Characteristics of Lead-Acid and Lithium Batteries
Lead-acid batteries are among the most widely used battery types and have a long history. They offer several advantages, including high tolerance to charging voltages, strong surge current capability, a wide operating temperature range, and low cost. Due to these characteristics, they are commonly used as starter batteries in vehicles, for powering forklifts, and in backup power systems.
However, they also come with some drawbacks, such as high self-discharge rates, heavy weight, and a relatively short cycle life of approximately 300 to 1,000 charge cycles, depending on the depth of discharge. As a result, they are less suitable for long-term energy storage solutions.
In contrast, lithium batteries offer a significantly longer cycle life of 1,000 to 3,000 charge cycles, lower self-discharge, and a higher energy density, making them ideal for long-term energy storage. Depending on the cathode material, different types of lithium batteries provide distinct properties:
- Lithium Cobalt Oxide (LCO) features high energy density, making it the preferred choice for consumer electronics.
- Lithium Iron Phosphate (LiFePO4) offers extended lifespan and high thermal stability, making it particularly suitable for energy storage applications.
One notable disadvantage of lithium batteries is the potential fire hazard in case of overheating. Therefore, precise monitoring during charging and discharging is essential to ensure safety.
Charging Parameters and Charging Curves for Batteries
The nominal voltage of a single lead-acid cell ranges from 1.8 to 2.3 V DC. Typically, these batteries are charged with a C-rate of 0.1C to 0.3C. In commercially available batteries, multiple cells are connected in series and parallel to achieve higher capacity and common output voltages such as 12 V, 24 V, or 48 V DC.
The designations "12 V," "24 V," or "48 V" serve as general voltage range indicators, as the actual voltage varies depending on the state of charge. For example, the open-circuit voltage of a 12 V lead-acid battery typically ranges between 10.8 V (30% battery capacity) and 13.8 V (100% battery capacity).
This dynamic voltage variation is directly related to the remaining battery capacity.
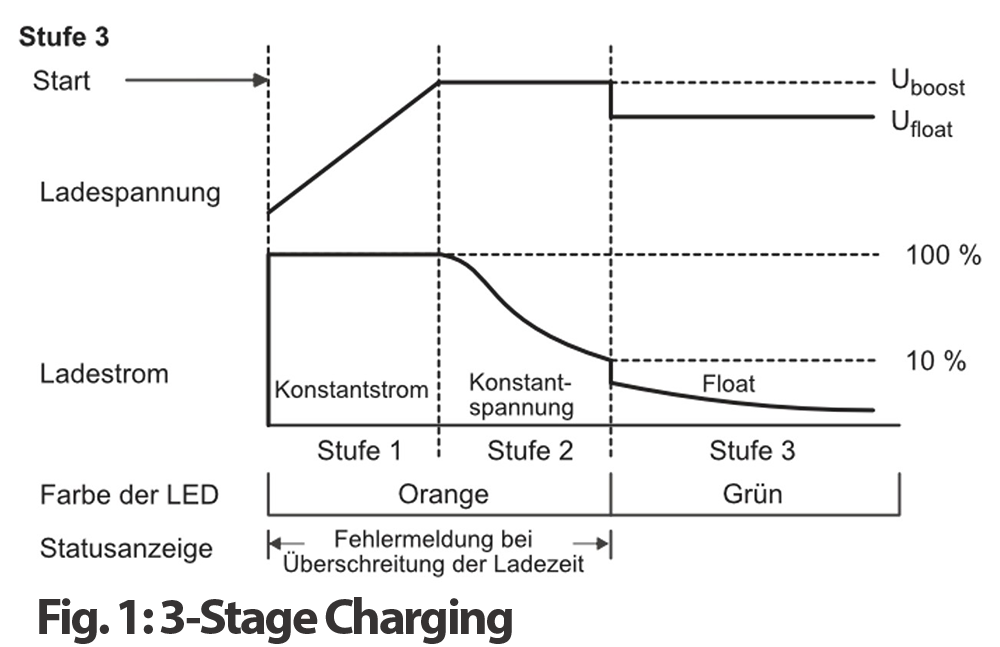
What Does the “C-Rate” Mean?
The C-rate (also known as the C-factor or C-coefficient) defines the relationship between the maximum allowable charge or discharge current and the battery’s capacity. This metric allows for a direct comparison between batteries of different capacities.
The inverse of the C-rate indicates the time required to fully charge or discharge a battery at maximum current.
- A C-rate of 1C means that the battery can be fully charged or discharged within one hour.
- A C-rate of 0.3C means that the charging process takes 3 hours and 20 minutes (1/0.3 h = 3.33 h = 3 h 20 min).
3-Stage Charging for Lead-Acid Batteries
Charging Parameters for Lithium Batteries
Lithium batteries have nominal voltages ranging from 3.2 V to 4.4 V and can be charged with a maximum C-rate of up to 1C. Even batteries with identical materials may have different nominal voltages and charging currents depending on the manufacturer.
Unlike lead-acid batteries, lithium batteries are sensitive to excessive charging voltage and do not require trickle charging to maintain their charge level. Therefore, charging is typically performed using a two-stage charging process (see Fig. 2), which eliminates the trickle charge stage.
Battery Management Systems (BMS) for Large Lithium Battery Banks
A common issue with large lithium battery banks is the variation in manufacturing tolerances among individual cells, leading to differences in equivalent series resistance (ESR). As a result, some cells within the same battery bank may charge and discharge at different voltages or currents. Cells with a lower ESR reach full capacity more quickly and degrade faster, which shortens the overall battery lifespan and increases the risk of thermal runaway.
To prevent these issues, large lithium battery banks should always be equipped with a Battery Management System (BMS). A BMS monitors the charge state of each individual cell and equalizes differences either passively or actively:
- Passive BMS: Fully charged cells are discharged through power resistors to match the charge level of the remaining cells. While this method is simple to implement, it is inefficient and less effective.
- Active BMS: Actively balances the charge of each cell, ensuring a uniform charge distribution. Because it controls the charging process for each individual cell, some lithium battery banks with an active balancing BMS can even be operated using a simple AC/DC power supply with constant voltage as a charger.
A well-calibrated BMS not only extends the lifespan and enhances the safety of lithium battery banks but also contributes to a more efficient and reliable energy supply.
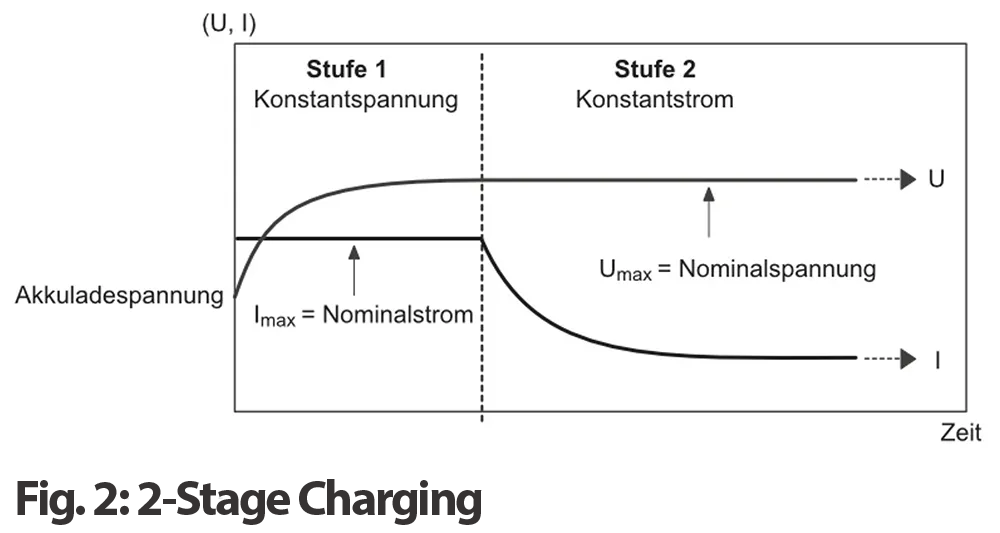
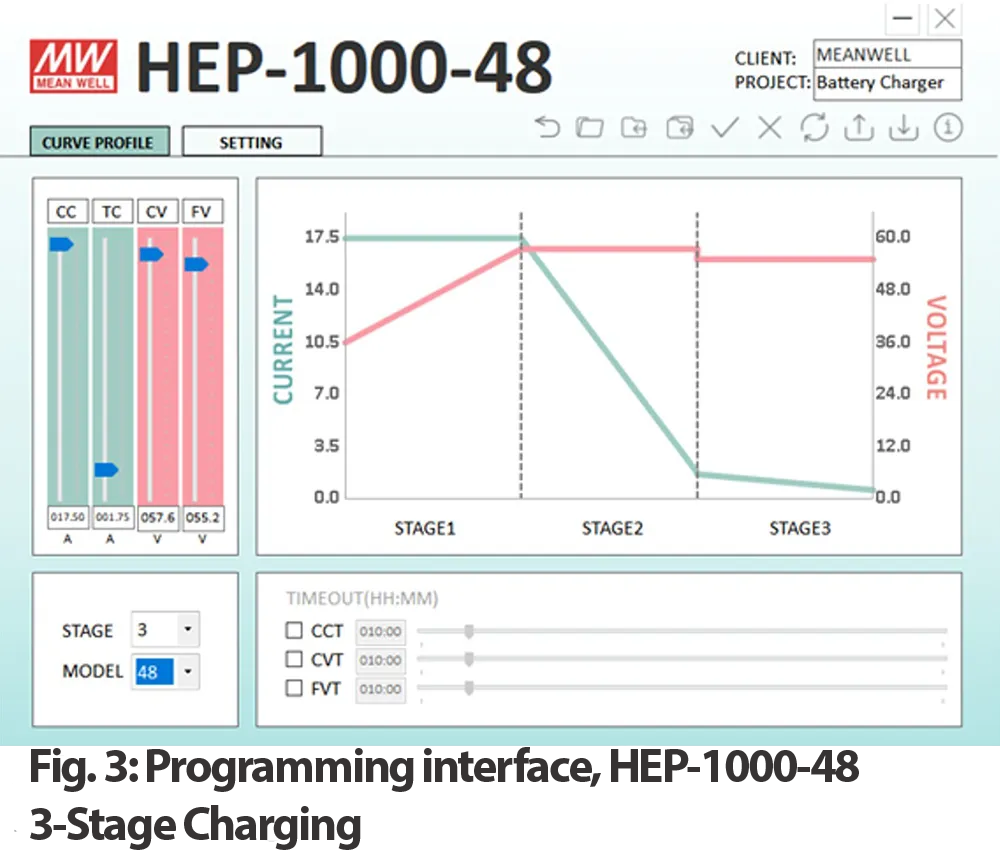
Programming Charging Curves and Parameters
Batteries with different compositions and from various manufacturers often have unique characteristics. To ensure reliability, longevity, and safety, it is recommended—and for lithium batteries, even mandatory—to optimize the charging curve accordingly.
The programmable chargers from MEAN WELL in the NPB-450/750/1200/1700, RPB-1600, RCB-1600, DBU-3200, DBR-3200, DRS-240/480, HEP-2300-55, and HEP-1000 series offer high flexibility and a user-friendly interface for customizing the charging curve when used with the SBP-001 intelligent programming device.
One example of a programmable charging curve is the HEP-1000-48, a well-established model. By default, it operates as a constant voltage power supply with 48 V DC and a maximum output of 1008 W. However, with the MEAN WELL Smart Charger Programmer SBP-001, it can be reprogrammed into a smart charger.
The default charging curve includes a 3-stage charging process (see Fig. 3) for lead-acid batteries, featuring:
- A boost charging voltage of 57.6 V DC
- A floating charging voltage of 55.2 V DC
For further customization, the charging voltage can be adjusted between 36 and 60 V DC, and the charging current can be set between 3.5 and 17.5 A to precisely meet the requirements of different lead-acid batteries.

Flexible Adjustment of Charging Curves for Lithium Batteries
Through the programming interface, the 3-stage charging process can be switched to a 2-stage charging process, making the HEP-1000-48 suitable for charging lithium batteries as well.
For example, a 20 Ah LiFePO4 battery with a maximum charging voltage of 56 V DC can be optimally charged by setting the "CV" (Constant Voltage) and "CC" (Constant Current) options to 56 V DC and 17.5 A, as shown in Figure 4. This configuration allows for the fastest possible charging.
Additionally, the user can:
- Reduce the charging current to prevent temperature increases caused by high currents.
- Lower the charging voltage to minimize the risk of overcharging the battery.
These customizable settings help maximize the safety, efficiency, and lifespan of the battery.